Ausgangslage und Aufgabenstellung
Die zentrale Anforderung des Kunden war der Austausch bestehender Rotationssiebmaschinen durch moderne Vibrationssiebmaschinen mit Ultraschalltechnologie. Ziel war es, mittels moderner Siebmaschinen, den Energieverbrauch zu senken und die Siebleistung zu erhöhen. Gleichzeitig mussten die Platzverhältnisse, die durch die vorhandenen Peripheriekomponenten vorgegeben wurden, berücksichtigt werden. Ein weiteres wichtiges Ziel war die Reduzierung des Ausschusses, der durch die Siebung entstand. Darüber hinaus mussten alle Umbauarbeiten den strengen Hygienestandards der Lebensmittelindustrie entsprechen und eine einfache Bedienung und Wartung der neuen Anlage ermöglichen.
Basic Engineering: Die Grundlage für ein erfolgreiches Projekt
Im ersten Schritt erfolgte das sogenannte Basic Engineering. Hierbei wurde die bestehende Anlagensituation detailliert aufgenommen und in einem 3D-Modell mittels Autodesk Inventor abgebildet. Diese virtuelle Darstellung ermöglichte es, verschiedene mögliche Konstellationen der neuen Anlage zu analysieren. Im Fokus standen dabei die Bedienerfreundlichkeit, die Wartungszugänglichkeit und die Sicherheit der Anlage. Auch die hygienegerechte Konstruktion war aufgrund der Anwendung im Lebensmittelbereich von entscheidender Bedeutung.
Ein wichtiger Aspekt dieser Phase war zudem die Prüfung von Anpassungsarbeiten an den örtlichen Gegebenheiten. Dies umfasste mögliche Änderungen am Stahlbau sowie die Anpassung bestehender Rohrleitungen. Zudem wurden in dieser Phase erste Grobkonstruktionen von Anlagenkomponenten wie Behältern, Treppen und Gestellen erstellt, um eine erste Kostenschätzung für das Projektbudget zu ermitteln. Die enge Zusammenarbeit mit dem Kunden war dabei essenziell. Sowohl die Produktionsmitarbeiter als auch die Instandhaltung und Anlagenbediener wurden intensiv in den Planungsprozess eingebunden. So konnte sichergestellt werden, dass die neue Anlage den Anforderungen und Vorstellungen aller Beteiligten gerecht wird.
Detail Engineering: Der nächste Schritt zur Realisierung
Nach Abschluss des Basic Engineerings ging es in die Detailplanungsphase. Das Detail Engineering konzentrierte sich auf die Ausarbeitung fertigungsgerechter Konstruktionszeichnungen, Aufstellpläne sowie die Erstellung von Stücklisten und Fließschemata (PID’s). Darüber hinaus unterstützten wir den Kunden bei der Elektroplanung der neuen Anlage, um die elektrische Integration reibungslos umzusetzen.
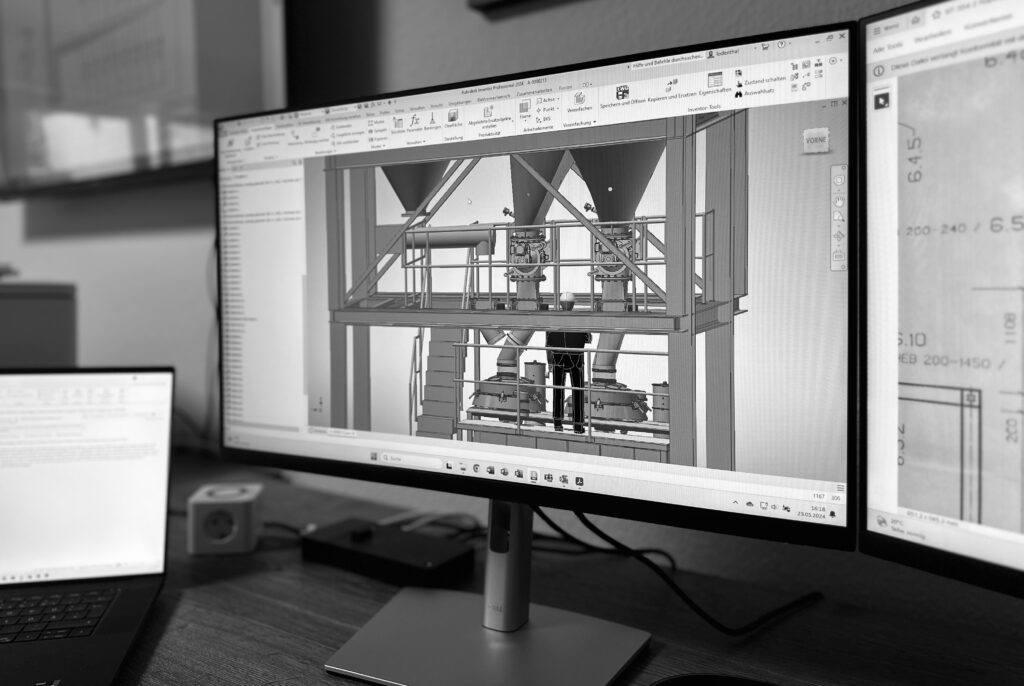
In dieser Phase wurden alle notwendigen Änderungen in Bezug auf Verfahrenstechnik, Elektrotechnik und Software auf die Anforderungen abgestimmt und den entsprechenden Abteilungen des Kunden zur Verfügung gestellt, um eine nahtlose Einbindung der neuen Komponenten in die bestehende Infrastruktur sicherzustellen. Dieser Schritt war entscheidend, um alle technischen Details festzulegen und die Grundlage für eine reibungslose Fertigung und Montage zu schaffen.
Montage der Neuanlage
Zunächst erfolgte die Demontage der Altanlagen, einschließlich der Behälter, Siebmaschinen und der zugehörigen Peripherie. Dies erforderte eine sorgfältige Planung, um bestehende Strukturen nicht zu beschädigen und den Stillstand der Produktion möglichst kurz zu halten.
Im Anschluss wurden Anpassarbeiten am vorhandenen Stahlbau vorgenommen. Hierzu gehörten Änderungen an Tragkonstruktionen, die Verstärkung bestehender Elemente sowie die Integration neuer Montagepunkte für die Neuanlage.
Die Montage der neuen Anlage umfasste den Einbau von Behältern, Zellenradschleusen und Siebmaschinen. Alle Komponenten wurden untereinander sowie an die bauseits vorhandene Peripherie angebunden. Eine präzise Ausrichtung und fachgerechte Installation stellten sicher, dass die Siebung effizient arbeitet und die geplanten Leistungssteigerungen erreicht werden.
Unterstützung während der Umsetzung
Neben dem Engineering und der Montage unterstützten wir den Kunden im Bestellwesen und der Terminverfolgung. Wir holten Angebote von Lieferanten ein, sodass der Kunde die Komponenten eigenständig bestellen konnte. Dadurch sparte er Preisaufschläge, die bei einer Bestellung durch uns angefallen wären.
Zudem übernahmen wir die Koordination der unterschiedlichen Gewerke, um einen reibungslosen Ablauf zu gewährleisten. Unsere Unterstützung umfasste ebenfalls die Überwachung der Montagefortschritte, die Abstimmung zwischen den beteiligten Fachbereichen und die Sicherstellung der Einhaltung von Arbeitssicherheitsrichtlinien.
Während der Umbauphase sorgten wir für eine transparente Kommunikation mit dem Kunden. Durch die enge Abstimmung aller Beteiligten wurde sichergestellt, dass auch kurzfristige Anpassungen reibungslos integriert werden konnten. Trotz Lieferverzögerungen gelang es, den Umbau der Siebung planmäßig abzuschließen und den Kampagnenstart termingerecht umzusetzen.
Erfolgreicher Projektabschluss und Ausblick
Das Projekt wurde erfolgreich abgeschlossen, und die Zielvorgaben wurden vollständig erfüllt. Ein herausragendes Ergebnis des Umbaus war die Steigerung der Produktionseffizienz: Durch den Einsatz der neuen Vibrationssiebmaschinen mit Ultraschalltechnologie konnte der Kunde nun 600 bis 800 kg Produkt pro Schicht zusätzlich gewinnen. Diese Menge bestand zuvor aus Ausschussware, die entsorgt werden musste. Dank der verbesserten Siebung kann dieses Material nun vollständig wiederverwendet und in den Produktionsprozess integriert werden, was zu einer erheblichen Reduzierung von Abfällen und einem effizienteren Ressourceneinsatz führt.
Der Kunde zeigte sich mit der Lösung sehr zufrieden und plant bereits den Umbau weiterer Siebanlagen in anderen Werken. Diese sollen ebenfalls in enger Zusammenarbeit mit uns realisiert werden. Das Projekt zeigt, wie durch den Einsatz modernster Technologie und eine durchdachte Planung sowohl die Energie- als auch die Ressourceneffizienz gesteigert werden können. Es wird auch deutlich, wie wichtig eine enge und vertrauensvolle Zusammenarbeit zwischen Kunde und Anlagenbauer ist, um maßgeschneiderte und nachhaltige Lösungen zu entwickeln.